As part of Boston University’s EK210 Intro to Engineering Design, a team of three other students and I were tasked with manufacturing and testing a 96-well microplate heater designed to keep tissue samples at a constant temperature of while the tissue was to be analyzed under an imaging microscope. The project was indented to simulate a real-world engineering scenario where a client presents us with a list of constraints and objectives that we are tasked with meeting. I was responsible for the mechanical design of the microplate heater. Keeping the design simple and without moving parts, which can increase the likelihood of failure, our team decided to embed a nichrome resistive wire into a clear acrylic base upon which the microplate is be placed. The nichrome wire is patterned around the microplate wells so that it does not obstruct the imaging microscope’s view of the samples. The microplate heater frame is made of 3D printed ABS plastic and the heating plate is made of CNC machined acrylic. I conducted thermal simulations in Autodesk Fusion 360 to estimate the performance of various nichrome wire pattern configurations and power outputs. The simulation predicted a deviation of across the entire acrylic heating surface for a power source, which matched our real-world tests. The nichrome heating element temperature is controlled by a MOSFET receiving PWM signals from a Atmega328p microcontroller with feedback from four NTC thermistor probes inserted into individual wells on the microplate. An LCD display on the heater shows the current temperatures in each well and the average temperature across all wells. Ultimately, our project was a success, as we met all the specifications that our client requested.
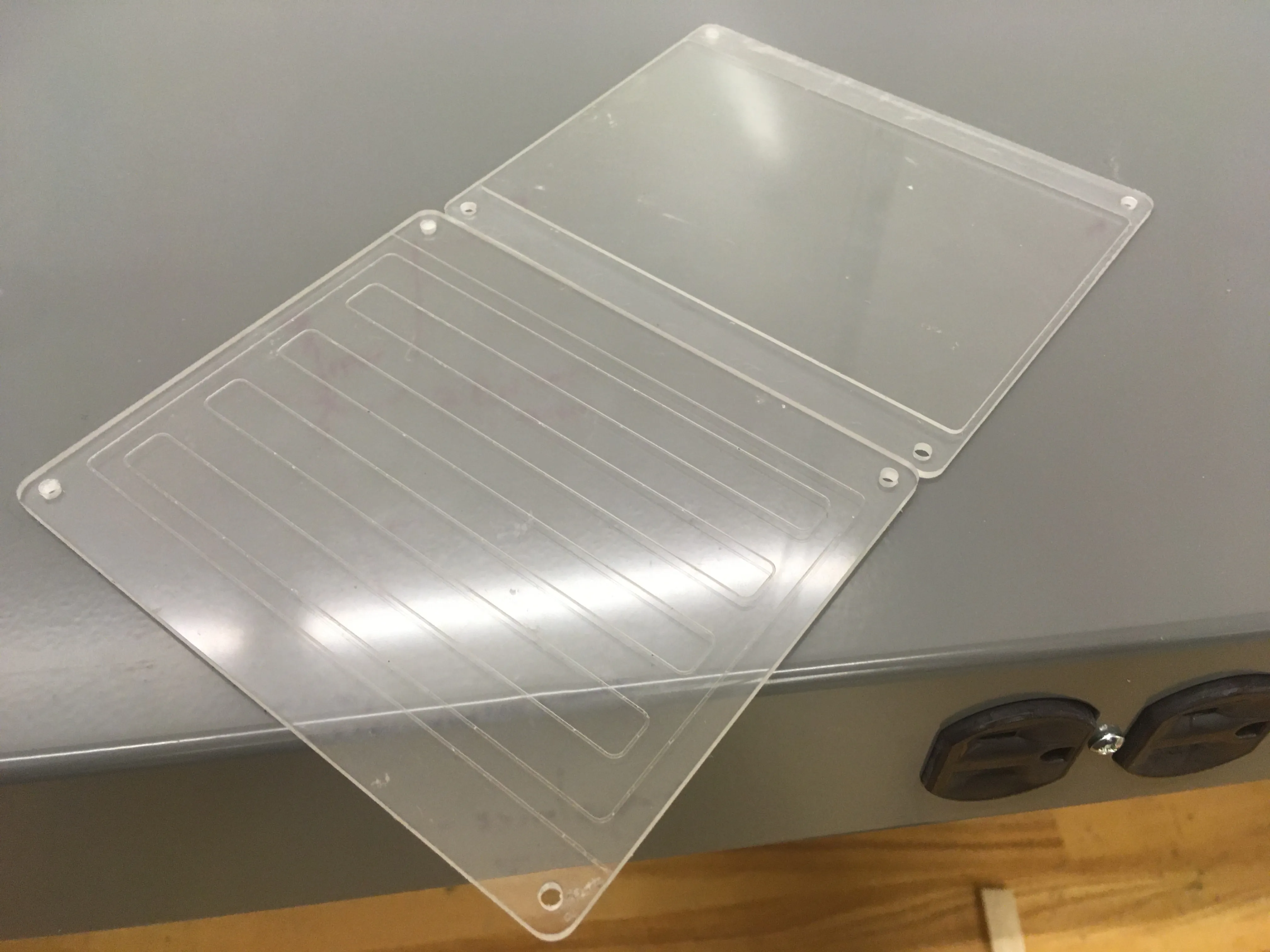
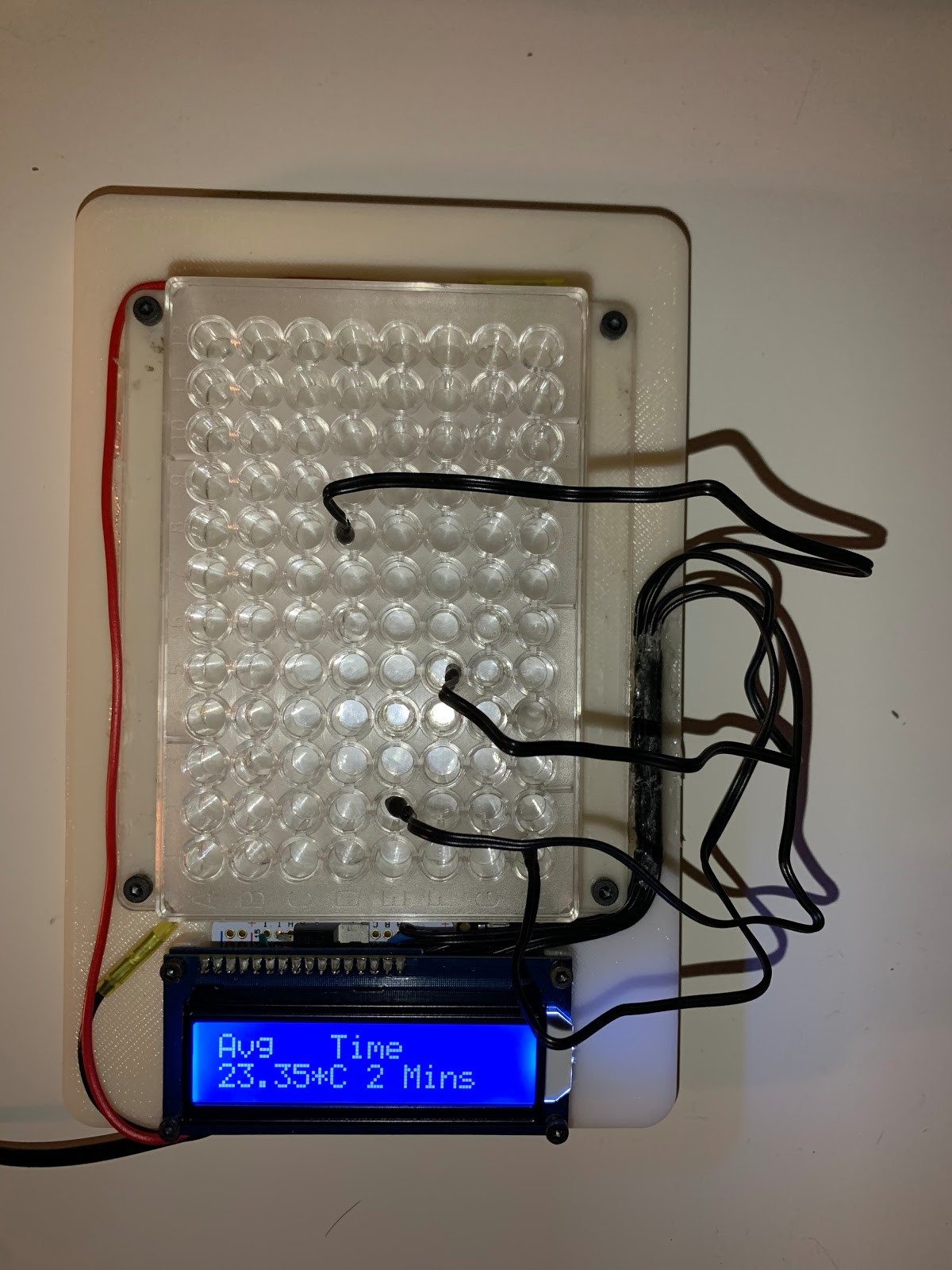
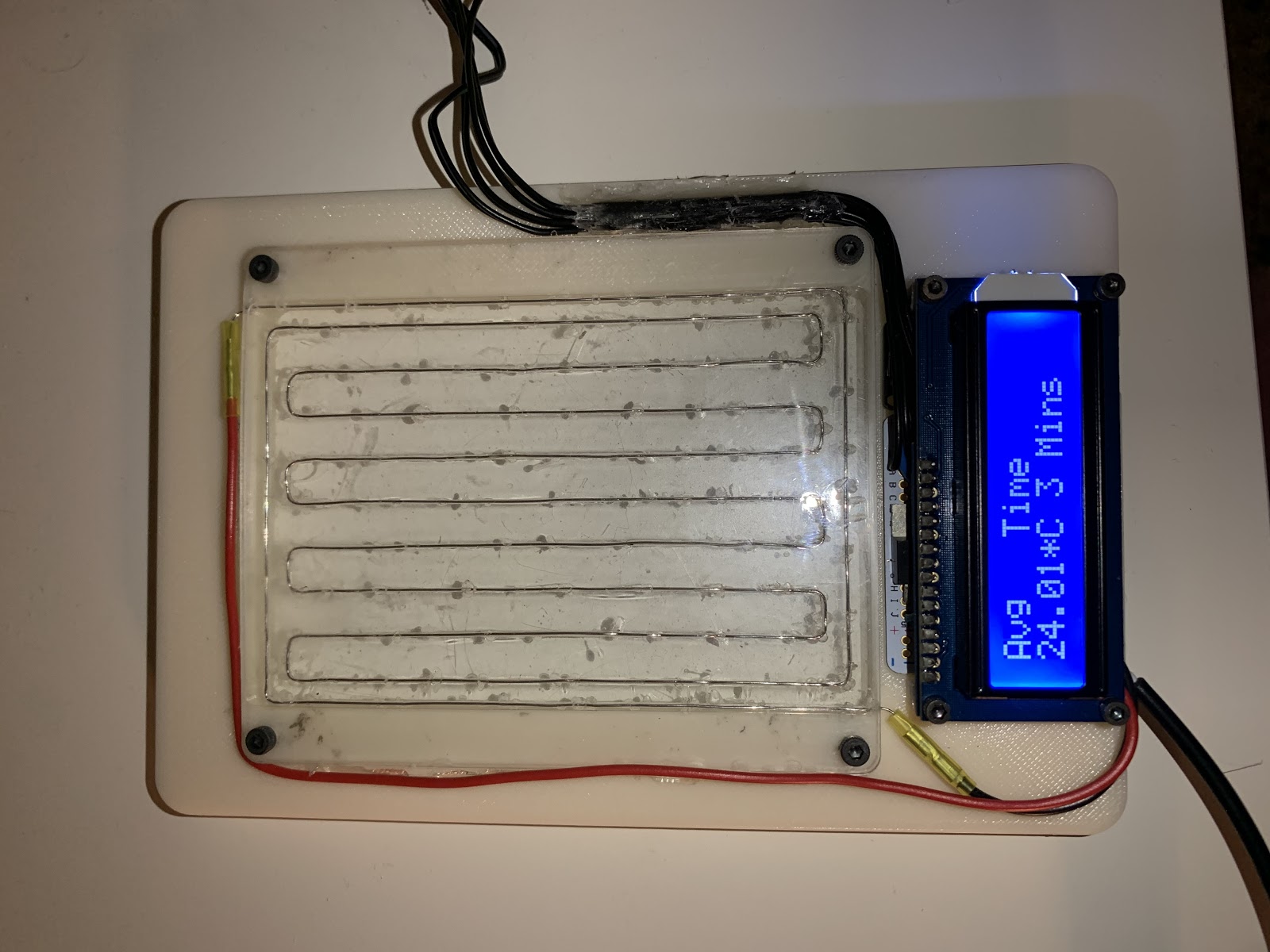
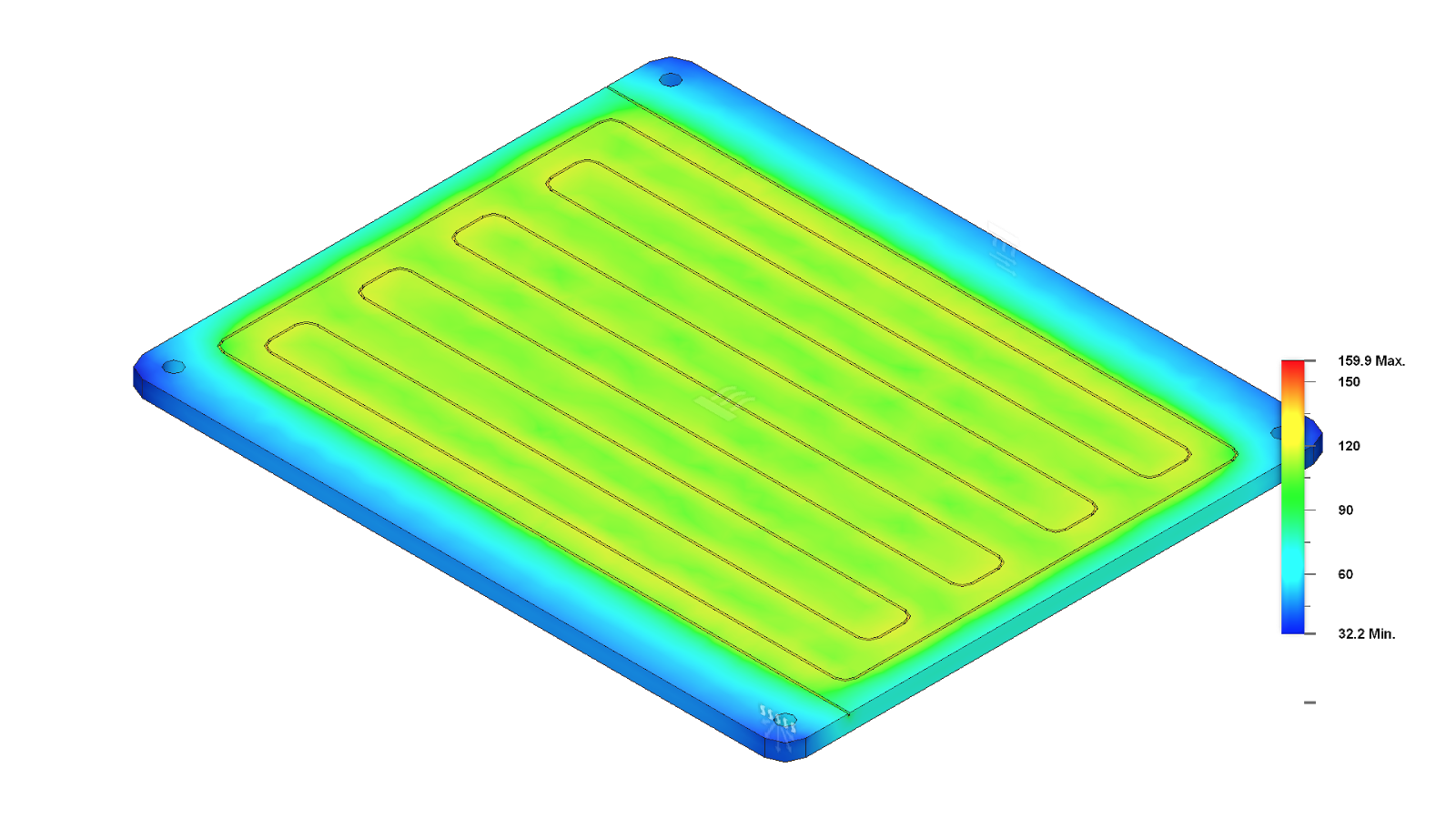
